Play: From Paper to Installation
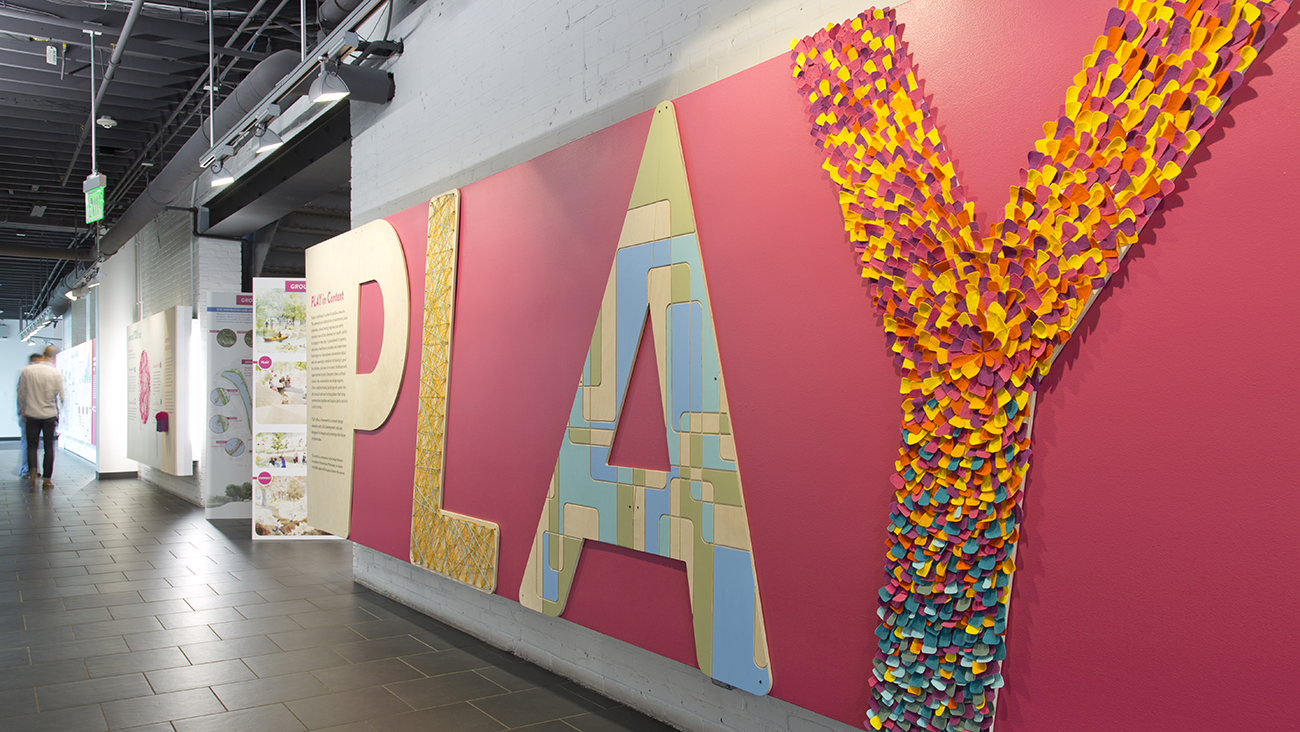
Visitors to Sasaki’s Watertown office this summer have been treated to an unlikely sight for a global planning and design firm. Larger-than-life letters, spelling P-L-A-Y, pop on a hot pink wall, decorated in patterns ranging from intricate networks of yarn to multi-colored felt feathers to blue and green abstractions.
This colorful creed isn’t just an indication of office culture, although this summer at Sasaki has been especially playful, it’s a hand-crafted introduction to PLAY, a gallery exhibit that explores the history of play and playscape design.
Springing from an internal research grant to conduct post-occupancy research on Smale Riverfront Park, the exhibition is as much a testament to the groundbreaking research and design going on at the firm as it is to the spirit and practice of collaboration at Sasaki. Bringing the firm’s play research to life took help from Sasaki’s graphic design department and the Fabrication Lab (Fab Lab). The team of graphic designers and the Fab Lab, with a little help from an out-of-house vinyl printer, transformed a research paper into a full-scale exhibit, complete with fill-in-the-blank questions, yarn fractals, and follow-along wooden mazes.
For the graphics team, the initial task was translating research into a visually-focused and human-sized exhibit. The graphics team chose a child-like color scheme of hot pink, baby blue, and forest green balanced with plywood material and domestic motifs to express the exhibit’s serious message regarding a playful topic. So viewers could play along, the graphics team also integrated participatory components—reinforcing the exhibit’s central contention that play is essential for healthy living.
Working with the Fab Lab allowed the graphic designers to experiment, especially on the interactive features in the installation—pushing the boundaries of what they could design and construct. For example, the two teams jointly determined the size of the panels based on the capacities of the machines in the Fab Lab. As graphic designer Ryan Collier reflected, “working in-house with the Fab Lab allows for a whole new level of exploration.” Architect Chris Hardy chimed in, adding that “the benefit of being able to realize your designs right away makes a world of difference to a designer.” Some members of the graphics team even participated in cutting the panels in the Fab Lab.
This close collaboration sparked experimentation for both teams. The graphics team could take ideas in new directions, conferring instantly with the Fab Lab on the feasibility of their ideas. On the other hand, working with the graphic designers who had little knowledge about fabrication processes jump-started the Fab Lab’s imagination. Reflecting on collaborating with the graphics team on the exhibit, architect Chris Winkler found that “working with someone who doesn’t understand the constraints of fabrication machinery is the best way to get ideas that push the boundaries. That childlike wonder of asking ‘why?’ or ‘why not?’ really helps us take down our blinders and find some interesting new approaches and workarounds.”
For the Fab Lab, fabricating the PLAY exhibition offered an opportunity to strengthen skills and expand knowledge. For the past year, the Fab Lab has been exploring design and fabrication possibilities via a CNC machine, laser cutter, 3D printers, and other tools. Each new project, like the PLAY exhibit, offers the Fab Lab a chance to test out new techniques like textures, patterns, and tool paths, and provides an opportunity to train others on the complex equipment. Winkler articulated the iterative process of working in the Fab Lab, “New projects allow us to expand our internal knowledge base of material properties and the results we can achieve with the tools that we have, informing our future project work.”
Principal Pablo Savid-Buteler, LEED AP, reflected on Sasaki’s fabrication practice and its pivotal influence on project work, “what we plan is inextricably tied to the lessons from what we build and vice versa. Our professionals are often involved with both ends of the planning to building spectrum. The Fab Lab in particular allows us to use physical and digital modeling as means to explore and visualize the possibilities of form and space making, to experiment directly with matter to understand material behavior, its possibilities and tolerances, and to prototype design solutions, testing iterations and verifying outcomes that can become standards or pilots for fabrication. Ultimately, it allows us to learn and create by making.”
After three months of brainstorming, designing, and fabricating, the gallery team installed the PLAY exhibit. Although the exhibit was meticulously planned, both the graphics and the Fab Lab teams continued to learn during installation. Director of Graphic Design, Terri Dubé, was most surprised by how many hours it took several people to hand-glue felt onto the letter ‘Y’ in PLAY—a task that was finished only a few hours before the exhibit’s opening. “We gleaned many valuable insights designing, iterating, and fabricating this exhibit. But perhaps the most important was something we never expected—the optimal assembly technique for attaching felt to plywood,” she said with a smile.